Latest interview: Network Manager Dr Cora Lüders-Theuerkauf and Strategic Advisor Stefanie Brickwede
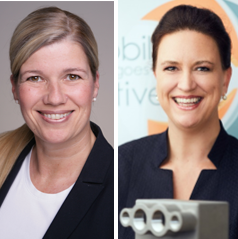
Dr Lüders-Theuerkauf, Ms Brickwede, the Medical goes Additive network offers a platform for its partners to develop and transfer knowledge in the field of additive manufacturing for the healthcare market. How did the idea for this network in the capital region come about?
S. Brickwede: The idea to found Medical goes Additive came from members of Mobility goes Additives (MgA) working with various AM technologies and materials development. In addition, AM technologies in medicine and medical technology are experiencing double-digit growth, more than is being seen in the industrial and automotive sectors. Especially in the capital region, there are numerous companies that are active creating applications in such medical as orthopaedics and dentistry. The Marienpark industrial park is currently developing the IAM Hub, a central point for additive manufacturing, with the MgA a key initiator.
Which stakeholders are going to find Medical goes Additive particularly interesting and why?
C. Lüders-Theuerkauf: Medical goes Additive is interesting for all users in the field of medicine, who want to begin looking at AM technologies and are looking for suitable partners. These include not only universities and research institutes, but also, in particular, SMEs with a strong focus on practical applications. The special thing about Medical goes Additive is its diverse membership: people active in such fields as orthopaedics, cardiology, neurosurgery, modelling (OR and training models), and medical device manufacturing seeing collaboration with printer manufacturers, printing companies, material and software developers, accreditation bodies, etc. and their desire to work together to find individual solutions to medical questions. These include increasing the awareness of how AM technologies can be used in medicine, working across industries on joint development projects, working together to shorten certification processes and develop markets and new business models. Many stakeholders don't yet know who their potential partners will be. This is where Medical goes Additives helps by establishing a single point of contact for AM in medicine and networking with international stakeholders, to build on and transfer their knowledge, and exploit synergies between markets.
In addition to the broad future potential, where do you see the greatest challenges for additive manufacturing processes in the medical sector? What options does the capital region offer?
C. Lüders-Theuerkauf: Some of the biggest challenges are the regulatory approval processes for medical products. The amendment to the Medical Devices Regulation (Regulation (EU) 2017/745), which came into force on 5 May 2017, imposes new mandatory guidelines. But for AM products, there often isn't a specific guideline available yet. Users need to work with legal advisors, regulators, and accredited bodies to make their effort worthwhile and ensure legal certainty for the manufacturing processes and products. Another challenge is the finding support for SMEs working in the medical sector. This not only includes financial support, but also, in particular, scientific and technological support with expertise and process chains. The capital region and its numerous networks and institutions like Berlin Partner that are active in promoting business and technology are a tremendous source of support.
Let's go a bit deeper. In addition to certification aspects, cost efficiency plays a major role for companies working in this field. In this context, the importance of (digital) supply chain management continues to grow. To what extent can a network offer significant added value here?
C. Lüders-Theuerkauf: The network, with its many members from different industries, has contacts that are often unavailable to an individual. This is the decisive added value for individual stakeholders, too. Common action requires bringing together potential partners, especially at the level of shortened certification processes. A platform in the form of a website and a newsletter also provides information about the activities of the network such as working groups, events, etc. as well as about the individual members themselves.
How does Germany and especially the capital region compare internationally when it comes to 3-D production technology? How will the technology and the applications evolve?
S. Brickwede: Germany is setting the global pace in AM technology. Many companies in the fields of printer production, printing services, and materials development are in Germany. The SME sector is also increasingly focusing on AM technologies and is gradually expanding or changing its conventional manufacturing processes, for example, from injection moulding to additive manufacturing processes. With increasing analysis of the processes and their end products, the qualitative comparability becomes clear with simultaneous time and cost savings. Especially for individual solutions, small production runs, and one-offs, additive manufacturing is a real innovation for medical technology. Additive manufacturing has recently also become the dominant process in such mass production runs as the manufacturing of hearing aids. The idea behind the AM technologies is to offer medical solutions that will become cost-effective, personalised, and fast, that will improve the treatment of patients and their quality of life in a sustainable way, and will reduce costs in medical practices and hospitals.
Is there anything you would still like to see in the legal framework?
C. Lüders-Theuerkauf: Shared rules both for the manufacturing and the final product are absolutely necessary. For this purpose, cooperation among users, providers, regulators, and licensing offices is essential. One example is the liability for AM manufactured products used in medicine. Clear legislation would simplify the industry's ability to act and allow manufacturers to obtain approval for high-quality, personalized new (medical) products with the goal of protecting patient safety and improving treatment options.